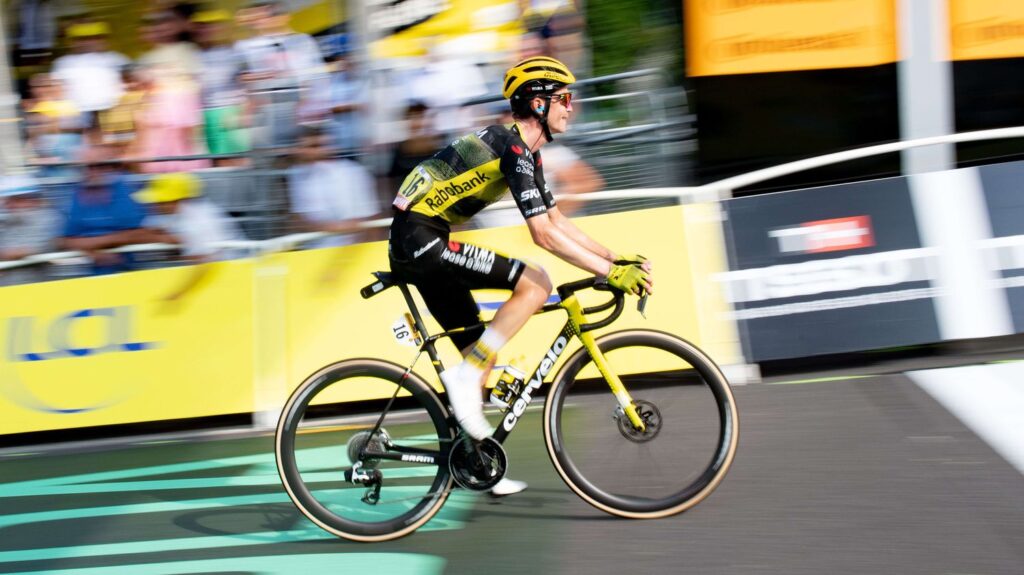
The equipment manufacturers have been competing in innovations for ten years to create ever faster bikes and outfits.
On the Tour de France, pedaling stronger is no longer enough to win. For a decade, the equipment manufacturers and bicycle manufacturers of the teams engaged on the big loop have been launched in a arms race with a simple goal: to make the riders the fastest possible. For this, they study bikes and outfits from every angle, to make small formula 1. “Even if I am retired, I drive faster today on the same routes as those on which I trained when I was professional”sums up Pierre Rolland (runner from 2007 to 2022).
Regardless of their physical preparation, professional runners have never been so rapid. “The aero (Understand aerodynamics) is worked on all the elements, whether it is the bicycle or the outfit, but also the cans or the positions of the runners “observes Pierre Rolland. Olympic track champion at the Paris Games, and therefore used to this quest for speed, the Frenchman Benjamin Thomas (Cofidis) confirms: “We are going to look for all the marginal gains in our training, equipment, nutrition … we try to optimize everything”. Starting with bikes, more and more sophisticated.
Like Slovenian Matej Mohoric (Bahrain-Victorious), some runners are very involved in the design of their mount. Which was also the case with Pierre Rolland, who confesses: “I was going to look for ceramic bearings, I could even invest my personal money for my bike. We can't change much in fact, but there are small things that can be changed slightly, cables, ducts, a chain, bearings”. But the bulk of the work goes to manufacturers, like the French company Lapierre, installed in Dijon since 1946, partner of the Picnic-Post NL of Warren Barguil.
“As in Formula 1, we are looking for excellence at all levels, marginal gains in the smallest detail, with continuous improvement”, explique Dorian Tabeau, Marketing manager of Lapierre, with whom six engineers work year -round on the Xelius DRS used by professionals. He adds: “From the 1980s, we saw a desire to perfect the equipment with Bernard Hinault. But it is since the 2010s, in the momentum of the Sky of Christopher Froome, that the quest for marginal gains has become central“. In a very competitive market, bicycle manufacturers who provide Tour teams such as Lapierre but also Specialized, Colnago, Look, Brain, Bianchi, Trek or Van Rysel, strengthened their teams with increasingly sharp engineers.
“Today you can lose a race if your bike is not fast. Chris Froome made it understand when he started attacking the descents.”
Dorian Tabeau, marketing manager at LapierreIn Franceinfo: Sport
The peloton bikes have thus become technological jewelry. The Lapierre Xelius DRS used by the runners of the Picnic-Post NL on this tower is thus composed of 560 pieces of carbon, distributed over the frame and the fork, with several different fibers depending on the needs (rigidity, lightness, dynamism, heat, etc.). A process that takes four hours of manufacture, for a bicycle of less than a kilo, before the installation of the other components. The minimum weight required by the UCI being 6.8 kg. “We, with the derailleur, the saddle, the wheels etc, we arrive at 7.3 kg”testifies Dorian Tabeau, recalling in passing “That there can be up to five brands on a bicycle, between the frame, the wheels, the tires, the saddle, the derailleur …”
“For a long time, we thought that the weight was most essential in a bicycle. While it is the aero that takes precedence. From 15 km/h, it's crucial, whether for sprints, descents, but also long ascents. This is why we stopped making bikes for sprinters and bikes for climbers, and we are only a single bike”testifies Dorian Tabeau, who specifies that his company is inspired by designs from aeronautics, before testing the bikes in the blower.
“Each part of the bike must be optimized as much as possible”, summarizes Dorian Table. “We put reinforcement patches in pierced places, a specific resin in the discs because it heats up, we have fibers for finesse, for comfort, for rigidity … They are sometimes superimposed. There are three areas of strong constraints: the pedals where all the power passes, the direction so that the bike is stable, and the back of the very rigid and reactive frame.”
“In three to six months, you can adapt the bike to the desires of the runners. Two runners can have the same bike in appearance, but not the same layer of carbon.”
Dorian Tabeau, marketing manager at LapierreIn Franceinfo: Sport
Axis of the wheels, GPS support, profiling of the rims and the fork, handlebars, seatpost, derailleur battery, bide holder … everything that exceeds the bicycle must create as little turbulence as possible in front of the wind. “While keeping a bike that meets the expectations of sprinters (rigidity, nervousness, speed), but also climbers (lightness, dynamism, reactivity), and by meeting the requirements of the teams”recalls Dorian Tabeau. A historic partner of Groupama-FDJ, the bicycle brand had to redraw the fork of its Xelius Drs last winter at the request of its new team, the Picnic-Post NL.
“We work in consultation with the staff and the team runners”says Dorian Tabeau, while recalling the importance for a manufacturer to provide a team engaged on the Tour de France: “You do not develop a good formula 1 without a pilot to drive it, and make feedback. Sponsor a team, it motivates the engineers, it pushes to go further. You will not put as much energy to develop a bicycle if not the big races. However, on these races, marginal gains can win, or lose. And then it allows us to offer the general public.
The nerve of war, the machines represent however only 10% of the overall aero of a runner on his bicycle, we explain at Lapierre, “The runner, himself, is 80% of the aero”. This explains why the textile equipment manufacturers are also launched in this race for innovation. Former professional runner, Stéphane Rossetto was thus hired by the French brand Ekoï when it comes down to the bicycle in 2022. “I assure the link between the brand and the athletes, to develop the textile collections'” explains the interested party. “I have the knowledge of the products since I have worn in my life more widers and jerseys than jeans,” he explains with humor.
“A runner has around 30 pieces of different textiles: gloves, shoe cover, socks, jackets, combinations, jerseys, vests … Each is studied to obtain aero and watts gains”, explains Stéphane Rossetto, before detailing: “They are very minimal on the gloves, it may even be more aero not to wear gloves. The most exposed place is the arms. The textiles in the back is also important, because this is where the air passes after the helmet, which is also very important. It is only at the level of the legs that we have no gain.”
To make the fastest outfits possible, reliefs almost invisible to the naked eye are drawn, while the fabrics are treated, explains Stéphane Rossetto: “It is as if we had frozen the fabric, which decreases the air resistance. We must also choose the right fabrics. There are always new products, so we make prototypes that we test in blower or outdoors on bikes clad in sensors. Each fabric reacts differently with each athlete according to his position, his corpulence …”. Without forgetting the thermoregulation imperatives, so that a runner is not too hot on his bike.
“The runners are moreover more obsessed with their aerodynamics, by data, food. But there are always counterexamples like Julian Alaphilippe, who has made all his career in a thigh jersey.”
Stepane rossettoIn Franceinfo: Sport
To the outfit then added the helmet, also studied in a blower to be aerodynamic without holding too hot, but also the glasses and the shoes. “Our glasses are designed to be worn with the helmet, and come together to be perfectly aero”specifies Stéphane Rossetto, whose brand Ekoï teams six training courses on the Tour de France 2025. But none took the bet to put on the last novelty of the brand: the chaussure pedal. “The hold is integrated into the sole, which means that we are much closer to the pedal axis, and therefore that we can lower the saddle a little and improve its aero position”explains Stéphane Rossetto.
However, these innovations come up against another race: that of security. “These are two incompatible things: we go faster and faster and at the same time, we say that we have to slow down”wonders Stéphane Rossetto, who is surprised to see runners carrying the time trial headsets on online stages. “I think it will not be long in being forbidden because it becomes a little anything. A chrono helmet, it protects less”.
“To reduce speed, you have to study the typologies of course, prohibit certain positions, regulate the size of the brackets.”
Dorian Tabeau, responsable marketingFrancanfo: Sports
“The example to follow, it's F1: when cars go too fast compared to the circuit, we do what it takes to slow down”pointed Marc Madiot in the program “Stade 2”, in May. “To slow down a bicycle, you could use wheels with flat rims, play on the weight of the frame, the brackets, have wider guides”. “This is a global subject, on which the instances do not listen to us, runners “regrets Benjamin Thomas, who believes that it should not be “Start technological progress, because it remains a mechanical sport. It takes a fair balance”. Integrated airbags inspired by mountain biking, no more resistant outfits: there is no shortage of tracks, and the innovations of tomorrow may be more on safety than speed.